Solar Panel Manufacturing Plant Cost in Pakistan
Pakistan, with its abundant sunshine, stands out as a prime location for the development of solar energy infrastructure. The establishment of a solar panel manufacturing plant in Pakistan offers substantial economic and environmental benefits, aligning with global trends toward sustainable energy. However, setting up such a plant involves considerable investment. This analysis delves into the various costs associated with setting up a solar panel manufacturing plant in Pakistan, exploring capital expenditure, operational costs, and the potential financial and logistical challenges involved.
1. Capital Expenditure
**a. *Land and Infrastructure Costs*: The initial capital expenditure for a solar panel manufacturing plant includes the cost of acquiring land and developing infrastructure. In Pakistan, the cost of industrial land varies significantly depending on the location. Urban areas like Lahore, Karachi, and Islamabad generally have higher land prices compared to rural areas. For a medium-sized plant, land costs can range from $500,000 to $2,000,000, depending on the size and location.
**b. *Construction and Facility Setup*: The construction of the manufacturing facility itself includes the cost of building structures, installing utilities, and setting up basic infrastructure such as roads and fencing. Building costs in Pakistan can vary, but a general estimate for constructing a facility of approximately 10,000 to 20,000 square meters is around $2,000,000 to $5,000,000. This includes expenses for industrial-grade buildings that can support the manufacturing process and associated utilities.
**c. *Machinery and Equipment*: The machinery and equipment required for solar panel manufacturing are substantial. Key equipment includes automated production lines for photovoltaic (PV) cells, laminators, testing devices, and quality control systems. The cost of these machines can range from $5,000,000 to $15,000,000, depending on the technology and production capacity. Importing advanced machinery can also lead to additional costs related to customs duties and transportation.
2. Operational Costs
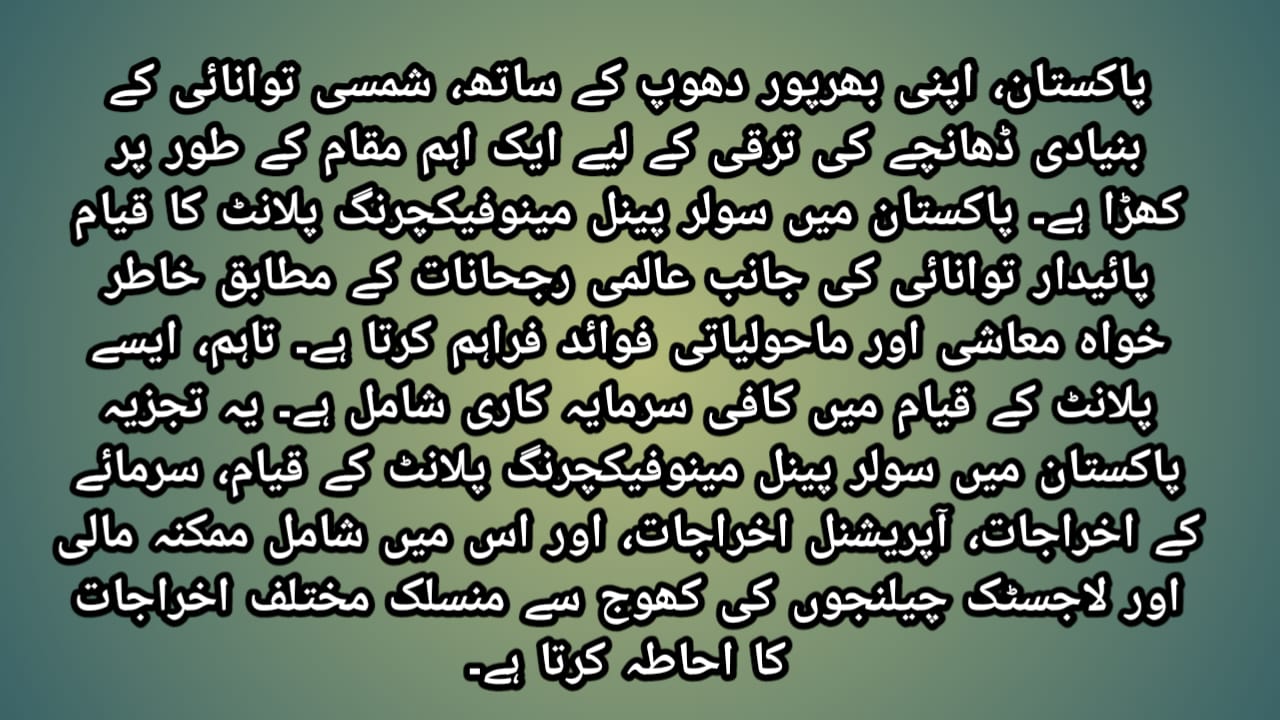
**a. *Raw Materials*: The primary raw materials for solar panel production include silicon wafers, glass, EVA film, and backsheet. While Pakistan has limited local production of these materials, they are often imported. The cost of raw materials can be substantial, potentially ranging from $10,000,000 to $20,000,000 annually for a medium-sized plant. Fluctuations in global prices and exchange rates can impact this cost.
**b. *Labor Costs*: Labor costs in Pakistan are relatively lower compared to many Western countries. Skilled labor, such as engineers, technicians, and operators, is crucial for maintaining high production standards. Average salaries for skilled workers in Pakistan can range from $500 to $1,500 per month. Considering the need for a skilled workforce of 50 to 100 employees, the annual labor cost might be between $300,000 and $1,500,000.
**c. *Utilities and Maintenance*: Manufacturing plants consume significant amounts of electricity and water. Utility costs can vary, but for a solar panel manufacturing plant, monthly utility expenses might range from $20,000 to $50,000. Maintenance costs, which include repairs and periodic upgrades to machinery, can also add to the overall operational budget, estimated at around $200,000 to $500,000 annually.
3. Financial and Logistical Challenges
**a. *Financing*: Securing financing for a solar panel manufacturing plant can be challenging. Banks and financial institutions may require detailed business plans and feasibility studies, and interest rates in Pakistan can impact the cost of loans. Public-private partnerships and government incentives can provide some relief, but navigating the financial landscape requires careful planning.
**b. *Regulatory and Compliance Costs*: Compliance with local regulations and standards is crucial. This includes obtaining necessary licenses, adhering to environmental regulations, and meeting quality standards. Regulatory compliance can add additional costs, estimated at around $100,000 to $300,000, depending on the complexity of the regulatory environment and the scale of the plant.
**c. *Supply Chain and Logistics*: Efficient supply chain management is essential to minimize costs. Importing raw materials and exporting finished products involves customs duties and logistics costs. These expenses can vary widely based on the location of suppliers and buyers, potentially adding 5% to 10% to the total cost of production.
4. Potential Benefits and Return on Investment
Despite the high initial costs, the long-term benefits of establishing a solar panel manufacturing plant in Pakistan can be substantial. The country’s abundant solar resources provide a ready market for solar panels, and government incentives aimed at promoting renewable energy can improve the financial viability of such projects. Additionally, local manufacturing can reduce reliance on imports, lower costs, and stimulate job creation.
Conclusion
Setting up a solar panel manufacturing plant in Pakistan involves significant capital investment and ongoing operational costs. The initial capital expenditure, including land, construction, and machinery, can range from $7,000,000 to $22,000,000. Operational costs, including raw materials, labor, utilities, and maintenance, add further financial considerations. Despite these challenges, the potential for growth and the positive impact on the local economy and environment make it a compelling investment opportunity. Careful planning, strategic financing, and leveraging government incentives can help mitigate costs and enhance the financial feasibility of such a venture in Pakistan.